1. Put the bottom cross beams on the platform longitudinally by 70° with the belt.
2. Put the water hydraulic plate on the bottom cross beams, and heat insulation plate upwards.
3. Put the bottom heating plate on the water hydraulic plate uniformly around it, with its working surface upwards.
4. Put the processed belt that dealt as per vulcanizing technique on the bottom heating plate, (if several vulcanizing presses work together, then a piece of about 0.3mm copper should be placed on the gap of each two vulcanizing presses). Meanwhile, install iron gasket bilaterally (the iron gasket are prepared by customers, which is about 75 mm width, but its thickness is thinner than belt about 0.5--1.0 mm, and longer than the vulcanizing press about 700mm). Then adjust to the same width as the belt by clamp devices.
5. Put the top heating plate on the processed belt, and the working surface is toward to belt, keep uniform with the bottom heating plate. If several vulcanizing presses work together, then a piece of 0.3mm thickness copper or steel sheet should be placed on the gap of each two vulcanizing presses.
6. Put the heat insulation plate on the top heating plate, and then put cross beams on
the heat insulation plate which keeps the uniform with the bottom cross beams. Install bolts, washes and screw the nuts by 30 KG/M moment to tighten evenly.
7. Connect control cabinet and heating plates with secondary cables, and connect power with primary cable.
8. Connect the water hydraulic plate and the (manual/electric) pump by high-pressure soft pipe.
The Installation of Conveyor Belt Vulcanizer
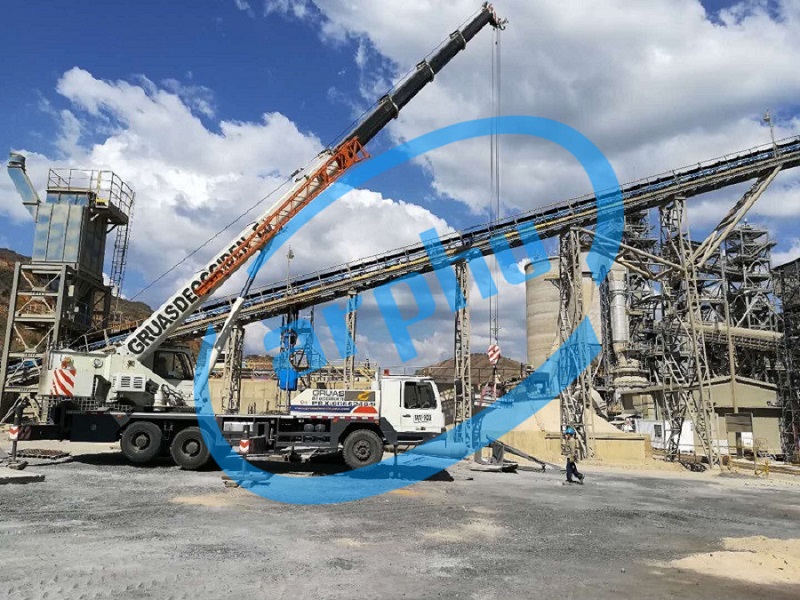